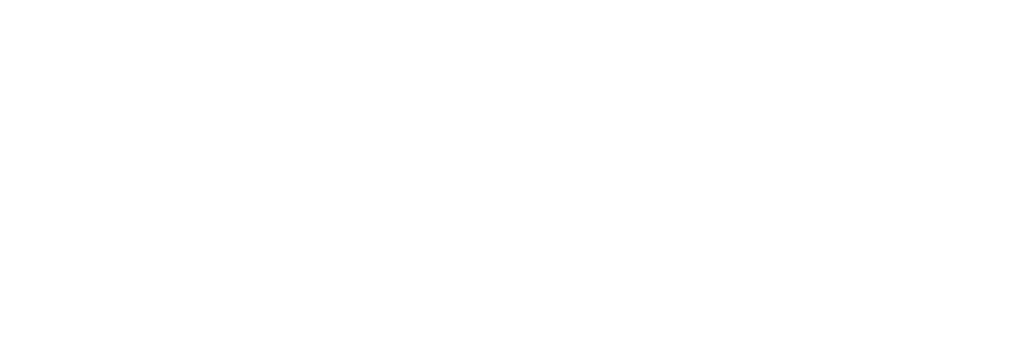
Aerodynamic tungsten coated mill technology for even wear, reduced no load power and long lasting performance. Proven kill of Australian Annual Ryegrass, the toughest weed to mill. Changeover time 20 minutes, simply slot in the latest mill tech and go.
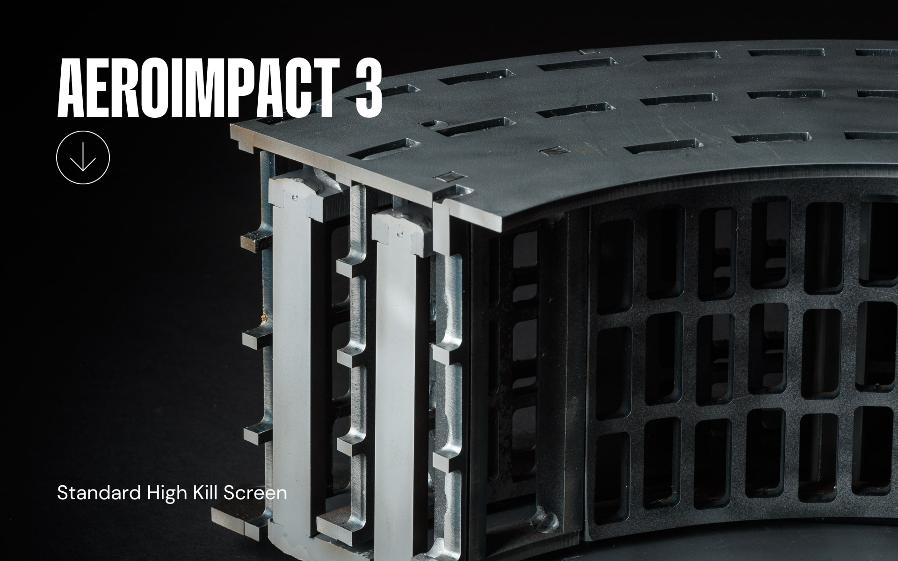
AeroIMPACT 3 : Standard High Kill Screen
KILL RATE: Ryegrass 99%
POWER: High
Used to kill 99% of weed seeds, ideal for cereals (especially barley) where grass control can be tricky. Given optimal harvesting conditions it is ideal for legumes where weed capture is at its highest.
Compatible with: AeroIMPACT 3 rotors & flails.
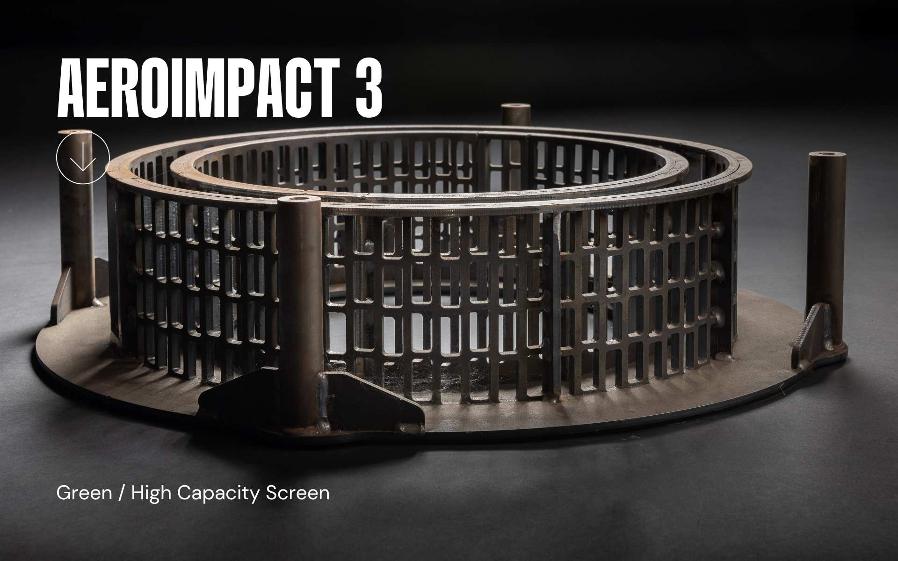
AeroIMPACT 3 : Green/High Capacity Screen
KILL RATE: 85-90%
POWER: Medium
Our High Capacity Screens have been designed to allow the operator to continue harvesting in tough conditions. Providing kill rates between 82-90% depending on mill speed and weed seed type. They are compatible with all Seed Terminator screen tech, and can be installed in 20 minutes. Optimal for crops with high moisture content, in green, tough or ropey conditions. Designed to prevent the mill blocking from the outside in.
Compatible with: AeroIMPACT 3 Rotors & Flails.
Look out for housing wear.
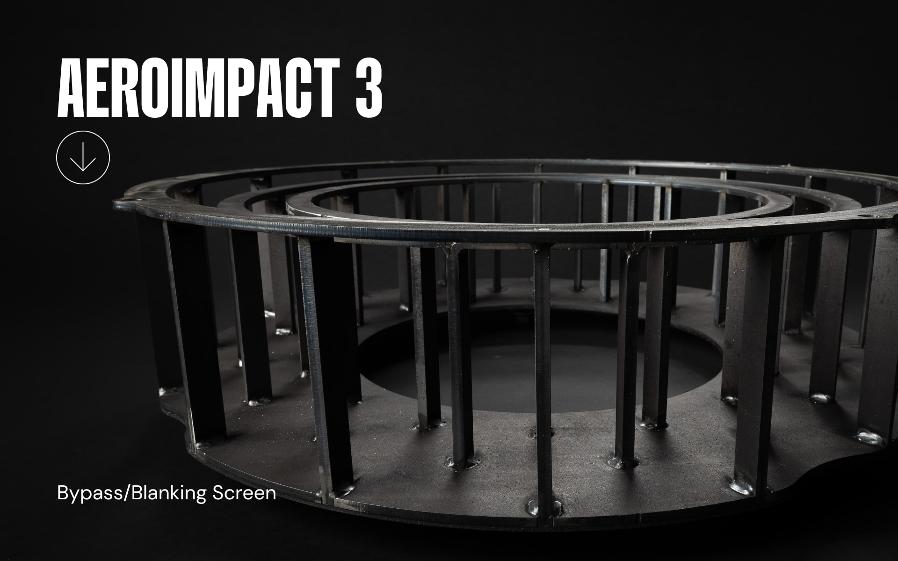
AeroIMPACT 3 : Bypass/Blanking Screen
KILL RATE: 50%
POWER: Low
Designed as a low power option, to target volunteers with a limited ryegrass control. Ideal for extreme harvesting conditions, or crops with low pressure of weeds.
Compatible with: AeroIMPACT 3 rotors & flails. Additional Suitability for CLAAS & New Holland in a bypass situation, with bonus volunteer kill.
Explore Rotors
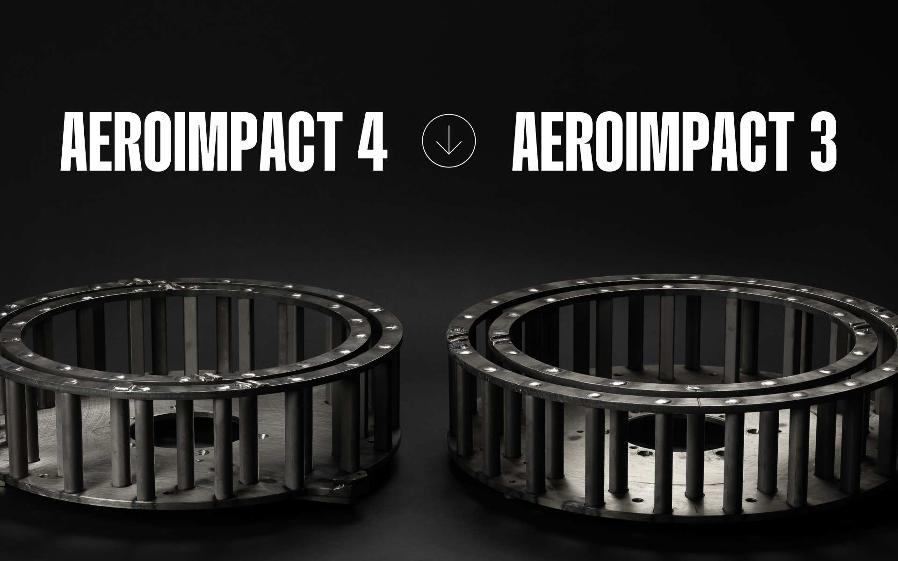
AeroIMPACT 3 versus AeroIMPACT 4
The AeroIMPACT 3 rotor is designed to maximise weed termination efficiency, featuring aerodynamic rotor bars that minimise no-load power to just 24kw, ensuring energy is focused on seed termination. At 300km an hour would you rather drive a truck or a Ferrari?
The AeroIMPACT 4 is the latest in efficiency built on the science of mechanically killing weeds. By tightening the tolerance between screen and rotor we’ve perfected each phase of termination, increasing capacity while maintaining kill.
Kill rate: Annual Ryegrass Lolium Rigidum 97%
Power: Medium
Compatible with: AeroIMPACT 4 rotors & flails
What are we made of?
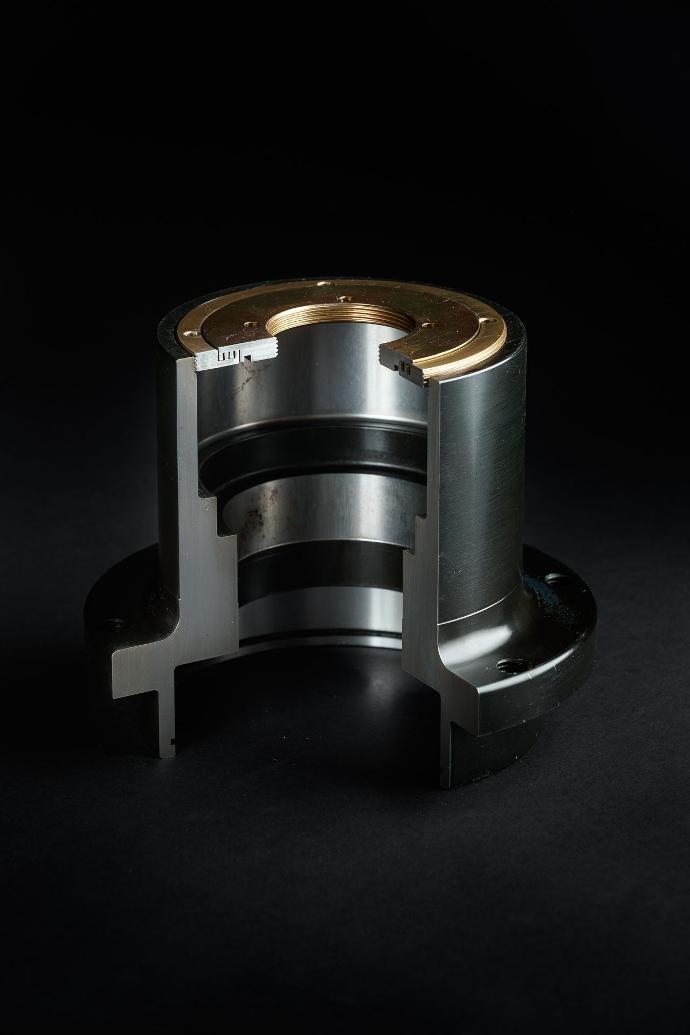

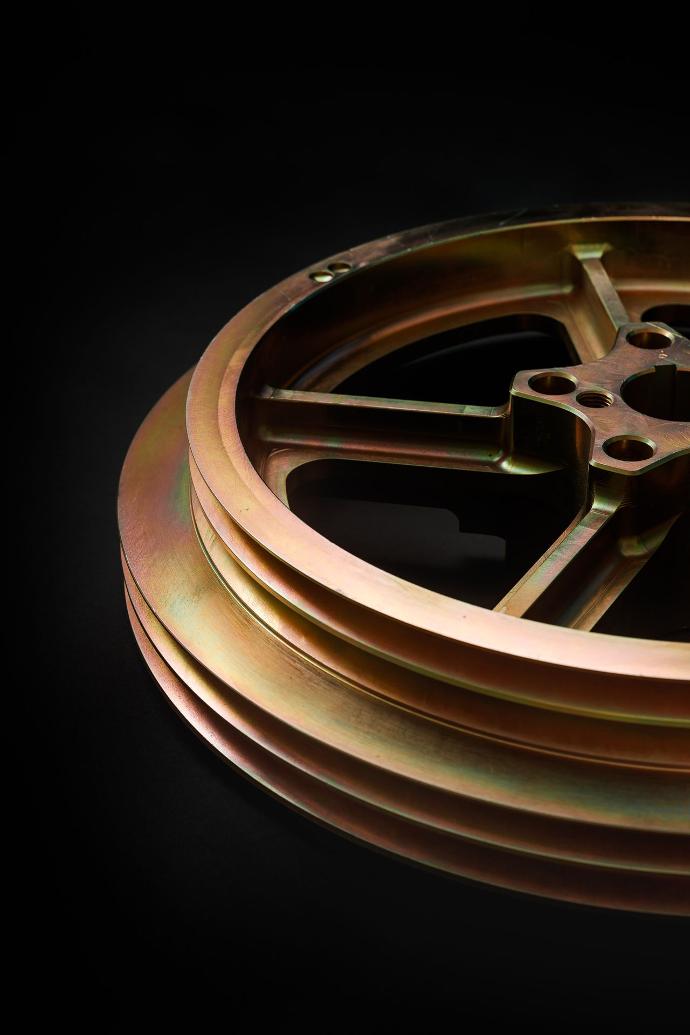
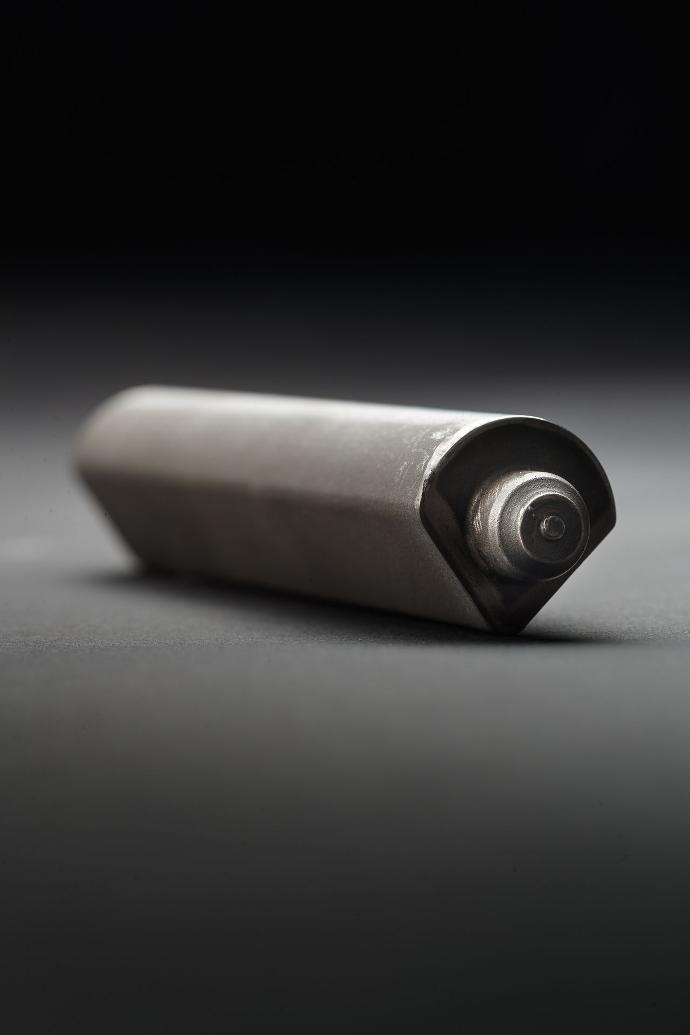
Join us in the workshop for Shop Talk. Brett Asphar walks us through measuring Screen, Rotor, and Flail wear on the Seed Terminator. He shows us how to measure wear and what and where to look for it.
Wear of AeroIMPACT 3
Screens range from 500 hours up to 1700 hours in really low wearing scenarios.
Rotors & Flails: from 1000 hours up to 3000 hours in really low wearing scenarios.
High Performance Screens like Bean Screen will wear quicker.
Wear of AeroIMPACT 4
Screens, Rotors & Flails for the Pro Series will wear together as the screens have been increased to a 10mm thick Australian steel Bisalloy 500, we are still gathering data on this with four harvests under our belt with this technology.
For the retrofit AeroIMPACT 4 on to Origin Series, the wear will be higher due to the higher throughput of material per hour.
Factors Influencing Wear
- Soil Type: Soil type significantly impacts wear, particularly when soil enters the machine. Harvesting low to the ground, which is effective for capturing more weed seeds, inevitably introduces more soil into the mills, accelerating wear. Some of the highest wearing environments are sandy soils with a high silica content, this is essentially sandblasting the components.
- Harvester Front Technology: The design of the harvester front plays a crucial role. A rigid front cutting low might collect more sand and other abrasive materials, leading to increased wear. Flexible fronts or stripper fronts, however, have shown to greatly enhance mill longevity by reducing the intake of abrasive materials.
- Harvest Speed: Faster harvesting speeds can cause the front of the harvester to bounce, leading to sand and soil being scooped up and thrown into the machinery. This can increase wear, especially when combined with certain types of cleaning fans which may exacerbate the issue.
- Crop Type: Different crops affect wear differently. For example, legumes tend to be harder on wear parts, while canola might help protect against wear. The need to harvest low to effectively capture weed seeds, which may be herbicide-resistant, necessitates adjustments in machinery use and settings to manage the increased wear.
- Processing Volunteer Grains off the sieves. The final factor influencing wear is one we'd prefer to keep in the grain tank! We've found if there was accelerated wear and its not due to sand intake the other culprit is processing grain off the sieves.
Managing Wear
- View wear and maintenance not just as a repair cost but as a necessary investment akin to purchasing chemicals for weed control. By understanding and adapting to the factors that influence wear, operations can be optimised to balance effectiveness in weed seed destruction with cost and equipment longevity.
Highest wearing regions in Australia
- Rainbow, Victoria due to sandy soils
- Pinnaroo, South Australia due to sandy soils and big lentil programs
- Balranald, New South Wales due to sandy soils
Aerodynamics and their role in no-load power
Aerodynamic rotor bars for lowest no-load power means more energy goes into killing seeds and less wasted energy making hot air.
As you can see from the images here, there is a turbulent wake behind the truck, creating hot air which is wasted energy. These aerodynamics (along with rolling friction) is largely why a truck uses more fuel/km than a sports car.
At Seed Terminator we spend a lot of energy manufacturing the profiles of our components and making them aerodynamic.
At 300km an hour the reduction in turbulence is compounded, allowing us to minimise the no load power.
Independent Testing Research
- ‘Optimisation of Seed Terminator settings in the South Australian Context’, 2019, Trengove Consulting, funded by South Australian Grains Industry Trust
- ‘Harvest weed-seed control continues to evolve’, 2017, Michael Walsh et al Western Australia.
- ‘Benchmarking Harvest Weed Seed Mills’ 2022, South Australian Grains Industry Trust funded Trengove Consulting, South Australia
- The University of Hohenheim in Germany
- The University of Missouri
Every year we are testing new mill technology, we have partners that we work with on an annual basis: The University of Adelaide Weed Science Research Group, Plant Science Consulting & Trengove Consulting.
^ South Australian Grains Industry Trust funded research into Weed seed control at normal operating speeds & settings. Stationary efficacy testing for Model Year 2017.
Generally we'd say 80-100hp is needed to run a mill.
Power and wear is the enemy, or is it?
If you are not using power or wearing material you are not killing weed seeds.
You can expect approximately 0.5 L/tonne more fuel in wheat. The theory says that the minimum fuel to kill 98% of weed seeds is 0.3L/tonne
- This doesn’t account for no load power
- Also doesn’t account for any chaff seed cushioning
Processing Power
How many seeds do you want to kill? The Energy to Kill weed seeds (ryegrass) from Nicks thesis, the energy to kill ryegrass seeds, damaging (vs reduced seedling emergence or kill) follows this curve. its not a step curve, as not all the seeds are the same. Below minimum energy there is no seed kill or damage.
“You can’t expect it to turn stuff into flour for no power draw cost”- Simon Reynolds, WA
Factors Influencing Wear
- Soil Type: Soil type significantly impacts wear, particularly when soil enters the machine. Harvesting low to the ground, which is effective for capturing more weed seeds, inevitably introduces more soil into the mills, accelerating wear. Some of the highest wearing environments are sandy soils with a high silica content, this is essentially sandblasting the components.
- Harvester Front Technology: The design of the harvester front plays a crucial role. A rigid front cutting low might collect more sand and other abrasive materials, leading to increased wear. Flexible fronts, however, have shown to greatly enhance mill longevity by reducing the intake of abrasive materials.
- Harvest Speed: Faster harvesting speeds can cause the front of the harvester to bounce, leading to sand and soil being scooped up and thrown into the machinery. This can increase wear, especially when combined with certain types of cleaning fans which may exacerbate the issue.
- Crop Type: Different crops affect wear differently. For example, legumes tend to be harder on wear parts, while canola might help protect against wear. The need to harvest low to effectively capture weed seeds, which may be herbicide-resistant, necessitates adjustments in machinery use and settings to manage the increased wear.
Managing Wear
- View wear and maintenance not just as a repair cost but as a necessary investment akin to purchasing chemicals for weed control. By understanding and adapting to the factors that influence wear, operations can be optimised to balance effectiveness in weed seed destruction with cost and equipment longevity.
Seed species is the most important parameter.
Seeds are of all different shapes, sizes and structure and therefore require totally different amounts of energy to control with a mill. Annual ryegrass (Lolium Rigidum) has been a major focus for testing, firstly because of its prevalence as a weed species, secondly because it is really hard to kill with a mill. This is due to its high fibre to starch ratio (meaning it is very tough) and because it is very light (hitting it doesn’t provide a lot of energy for seed damage).
When it comes to Ryegrass, seed size is an important factor
Researcher Sam Trengove of Trengove Consulting is collating data on in paddock Annual Ryegrass Seed Size across Australia. Initial results indicate there is a viable range of seeds from 1.1mg per seed to 3.2mg per seed, with the median size being 2.6. Due to the hard to kill nature of ryegrass, the smaller the seed the harder it is to kill (as above - hitting it doesn’t provide a lot of energy for seed damage). Most testing done in the past decade has been done on seeds in the 2.8-3.2mg per seed range.
Mill speed & Moisture content
When relying on a single mode of action, such as impact, changes in moisture content can affect seed resistance to impact, leading to a reduced kill rate. Additionally, drops in mill speed can also decrease the effectiveness of seed kill. When both factors occur together, the reduction in seed kill can be significant.
The graph below shows the effect of weed seed moisture content when relying on impact alone for Reduced Seedling Emergence (RSE% or kill), for example the red line shows 4 impacts at 70 meters per second; at 10% moisture content it has high RSE or kill, but at 13% moisture it drops to 90% and at 17% moisture the kill is 70%.
What does this mean? In high moisture content scenarios impact alone has significantly reduced efficacy. The second point here is that if there was a drop in mill speed, relying on impact alone, the green line shows 4 impacts at 50 meters per second at 10% moisture the kill is just over 60%.
What does that mean for Seed Terminator? The Multistage Hammer Mill Technology has three stages of screens. Multiple stages enable high capacity while maintaining pulverisation to consistent level at a range of rotational speeds.
.
Listen to Nick's podcast 'The journey of designing a mill'